Piątek
6 rano…. pobudka, kawa, kanapki zabrane z recepcji i ruszamy do firmy producenta maszyn. O 7 rano jesteśmy na miejscu. Kierownictwo już znamy z wcześniejszych targów branżowych, więc zaraz po krótkim zwiedzaniu firmy udajemy się do laboratorium celem rozpoczęcia testów.
Z tyłu głowy silne uczucie i świadomość kilku godzin jakie mamy na znalezienie rozwiązania. Po szczegółowym omówieniu tematu – pada hasło: „dobra teraz dokładnie wiemy, czego chcecie, będzie ciężko, ale próbujemy”. Nie tracimy czasu, rozpoczynamy testy. Technik laborant opierając się na swoim doświadczeniu, określa ramy czasowe, typ, model i kształt poszczególnych wsadów, których należy użyć. Wszystkie działania koordynuje kierownik produkcji. Uczestniczymy w tej rozmowie żywiołowo. Chcemy sprawdzić każdą ewentualność, która narzuca się na myśl. Nie ma czasu na zastanawianie się co do merytorycznej zasadności pytań. Kierujemy się zasadą: „nie ma głupich pytań, są tylko głupie odpowiedzi”. Średnio, co 20-30 minut dostajemy kolejne partie przeprocesowanych modeli w rożnych kombinacjach co do rodzaju wsadu, czasu procesu, prędkości obrotowej maszyny i ilości dozowanej wody. Weryfikujemy każdą partię, dyskutujemy, staramy się znaleźć najlepszy balans pomiędzy ustalonym czasem procesu a efektem końcowym obróbki powierzchni obudów aparatów słuchowych.
Popołudnie staje się faktem szybciej niż się tego spodziewaliśmy. Pozostały nam dwie, może niecałe trzy godziny. I jesteśmy blisko….. pojawia się uśmiech na twarzach. Ale chcemy więcej, chcemy uzyskać maksymalny efekt przy spełnieniu wszystkich restrykcji procesowych. Tuż przed głównym wejściem do firmy widzimy ciężarówkę, do której producent pakuje swoje maszyny na rozpoczynające się od kolejnego poniedziałku targi branżowe. To sprawia, że nasza wyobraźnia sprowadza nas błyskawicznie do rzeczywistości, pozbawiając resztek nadziei na magiczne przedłużenie wizyty o kolejny dzień wobec braku satysfakcjonującego rozwiązania dzisiaj.
Kolejne testy i w końcu z wyrazu naszych twarzy możemy jasno wyczytać: „Mamy to”. Wprawdzie nie jest to 100%. ale znacząco dużo w porównaniu z tym, co obecnie uzyskujemy po procesie obróbki wygładzarkami odśrodkowymi. W tyle głowy kotłuje się radość z uzyskanych rezultatów jednak wciąż przeplatana obawą o zachowanie odpowiedniej grubości ścianek testowanych modeli. Mierzymy wylosowaną próbę, jest OK. Oddech – ponownie uśmiech i zdrowa satysfakcja przesłania już niedawną niepewność. Zbieramy próbki i zakupione nowe materiały, podejmujemy wstępną decyzję o zakupie dodatkowych maszyn, wreszcie żegnamy się z przedstawicielami firmy i wracamy do domu.
Rozpoczyna się weekend – czas na odpoczynek, życie prywatne i zebranie myśli. Wiemy, że w poniedziałek przedstawimy kierownictwu rezultaty przeprowadzonych testów i cały ogrom pracy związany ze szczegółowym opracowaniem nowego procesu jest dopiero przed nami. Nabierze to wszystko jeszcze większego tempa niż dotychczas bo oprócz znalezienia rozwiązania, na pierwszy plan wysuwa się teraz czas wdrożenia nowego procesu (oczywiście po szczegółowym zweryfikowaniu i jednoznacznym wykluczeniu wszystkich ewentualnych nieprawidłowości). I to jest ten stan, kiedy własna satysfakcja zawodowa przysłania wszystko inne, co nie jest teraz istotne. Patrząc z jednej strony można rzec: „A tam po prostu zwykła, ludzka satysfakcja z realizacji powierzonego zadania i wywiązania się z przydzielonych obowiązków służbowych". Zgadzam się, można. Jednak patrząc z drugiej strony, można również łatwo dostrzec, że ta zwykła, ludzka satysfakcja ma znamiona niezwykłej, bo daje motor i paliwo do realizacji kolejnych zadań, stawiania czoła nowym zadaniom i wyzwaniom, ale już z kolejną cegiełką umacniającą świadomość własnych kwalifikacji i zaufania do siebie samego i względem zaangażowanych osób.
Na koniec…. tak sobie myślę, że pewnie wielu Wam, którzy zdecydowali się poświęcić chwilę na przeczytanie tego artykułu, narzuca się jedno zasadnicze pytanie. „Co to za usprawnienie? Zakup dodatkowych maszyn i wydłużenie czasu procesu trzykrotnie z jeszcze dodatkowym rozdzieleniem na dwie podoperacje”. Rozumiem. Należy jednak zwrócić uwagę na jeden istotny fakt. Otóż, celem optymalizacji nie było skrócenie samego procesu. Celem było zoptymalizowanie procesu do tego stopnia, aby możliwie jak najmniej czasu tracić na proces obróbki obudów aparatów słuchowych bezpośrednio na linii produkcyjnej. Innymi słowy, istotą wprowadzonego obecnie rozwiązania w zakresie wygładzarek odśrodkowych jest eliminacja potrzeby, ewentualnie skrócenie do możliwego minimum – czasu ręcznego szlifowania każdej obudowy na linii produkcyjnej.
Należy również uczciwie powiedzieć, że wprawdzie 100% nie zostało jeszcze osiągnięte i być może nie będzie jeszcze długo (bariery technologiczne, np. różnorodność modeli aparatów, kształtów, rodzaju koloru żywicy – różny kolor i inne, pewne właściwości fizyczno-chemiczne żywicy, a więc jej właściwości na ścieralność i obróbkę procesową). Ale na koniec możemy zgodnie powiedzieć, że wartość na poziomie 70% jest wiarygodnym wynikiem nowego procesu dla usunięcia ilości linii papilarnych ze wszystkich modeli wkładek obudów aparatów słuchowych. Rezultaty wprowadzonej optymalizacji procesu, doskonale obrazują poniższe zdjęcia oraz porównanie standardowego i nowego procesu.
1. Shell po standardowym procesie
Rodzaj procesu: gratowanie; rodzaj użytego wsadu: kształtki ceramiczne; czas procesu: 15 minut
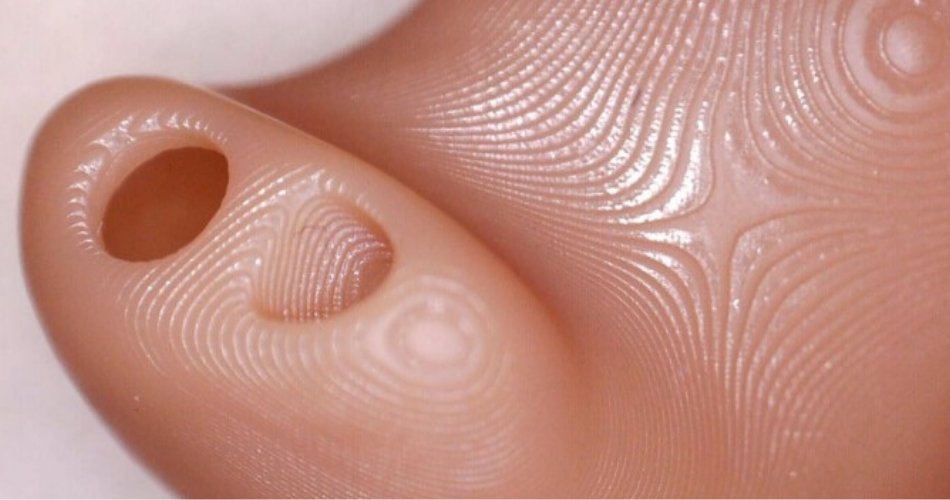
2. Ręczny proces obróbki na linii produkcyjnej bez użycia wygładzarek odśrodkowych
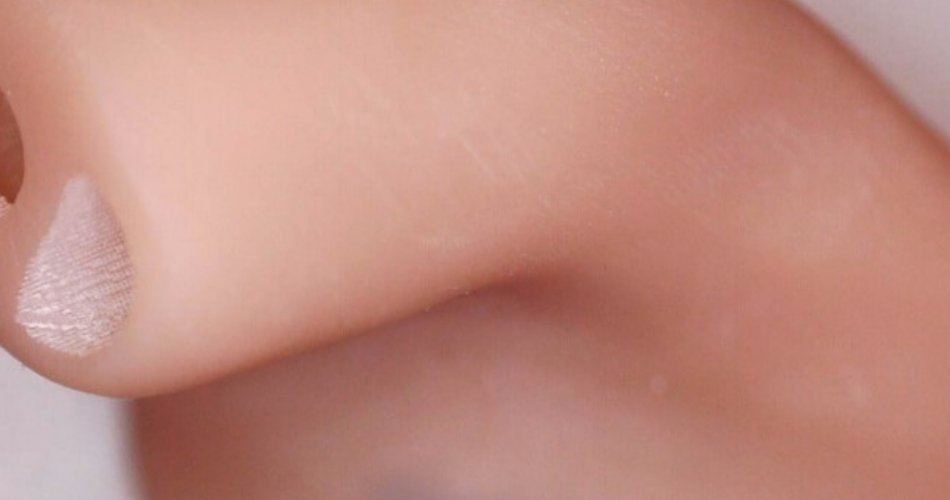
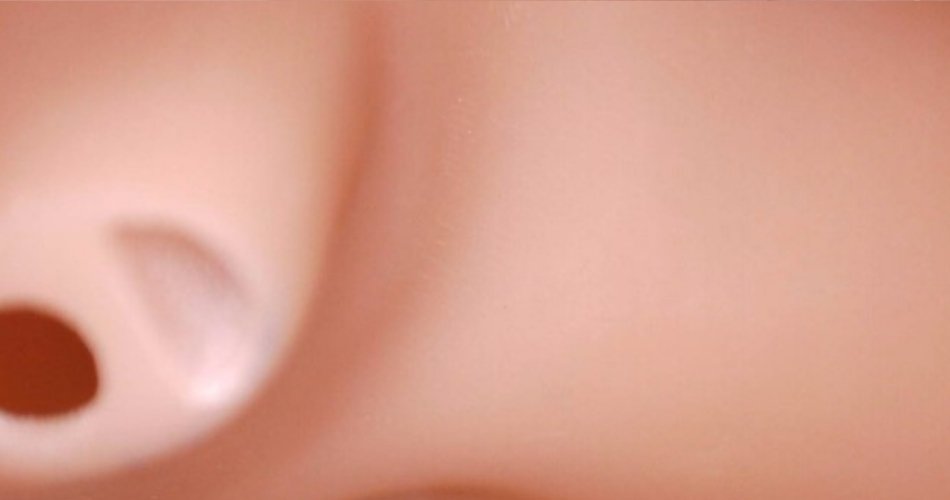
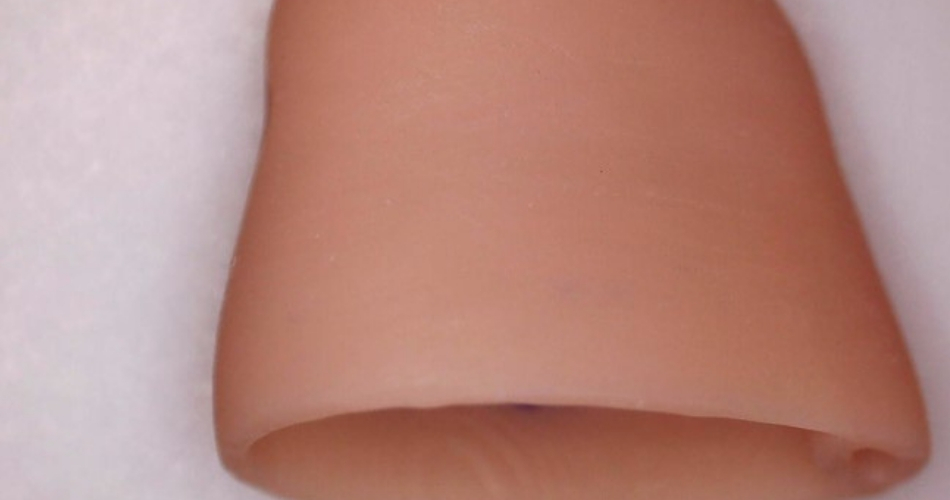
3. Shell po nowym procesie.
(1) rodzaj procesu: gratowanie, rodzaj użytego wsadu: kształtki ceramiczne; czas procesu: 45 minut
(2) rodzaj procesu: szlifowanie, rodzaj użytego wsadu: kształtki żywiczne, czas procesu: 45 minut
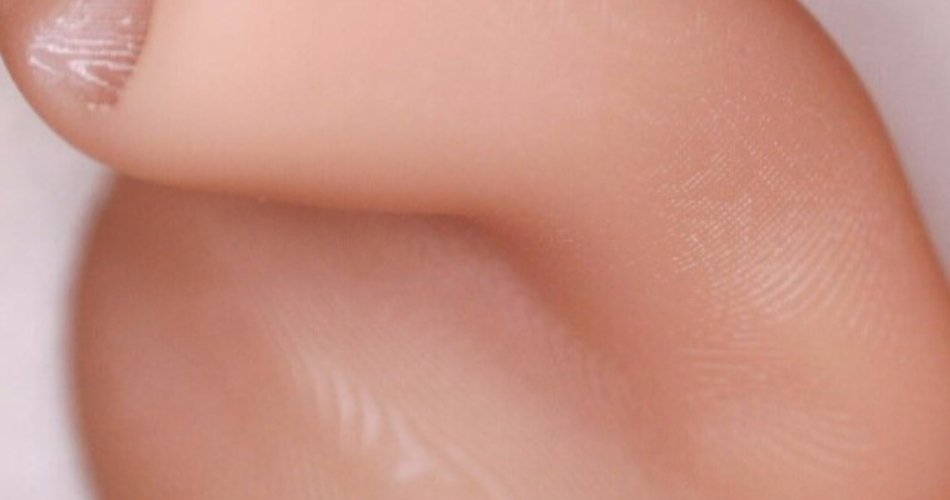
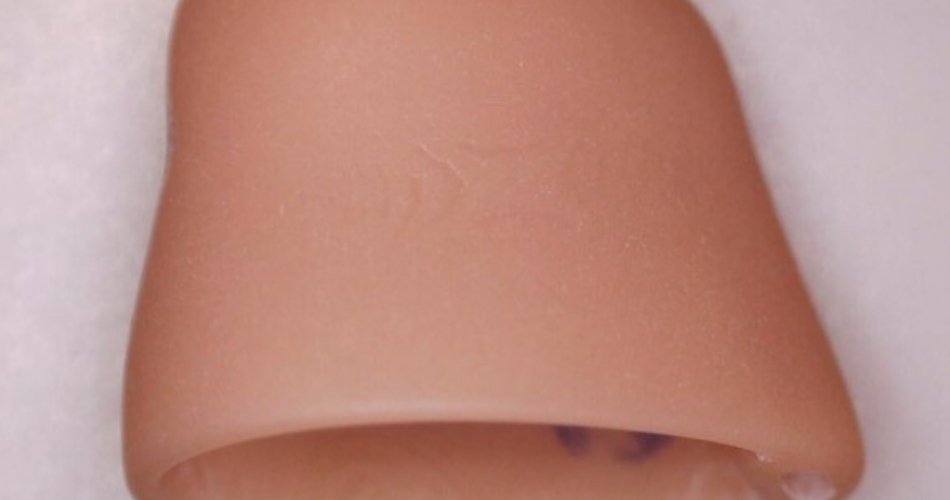
Porównanie standardowego i nowego procesu obróbki powierzchni wygładzarkami odśrodkowymi
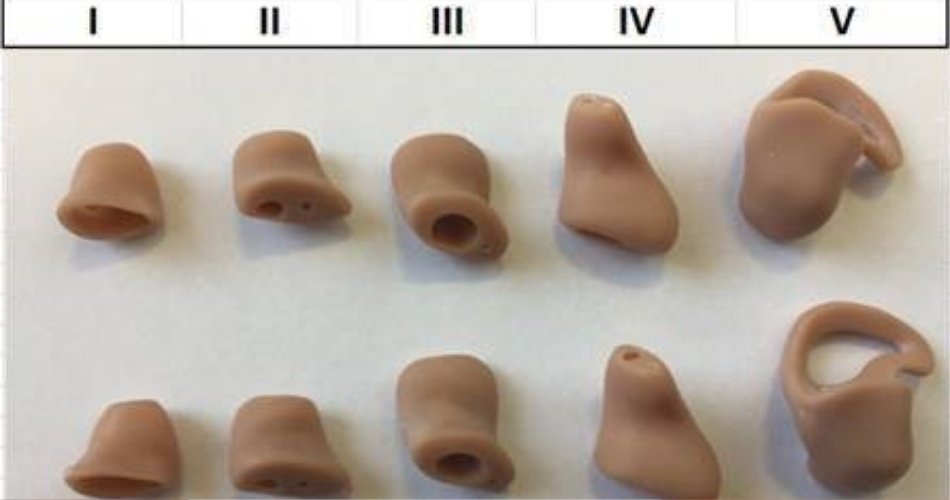
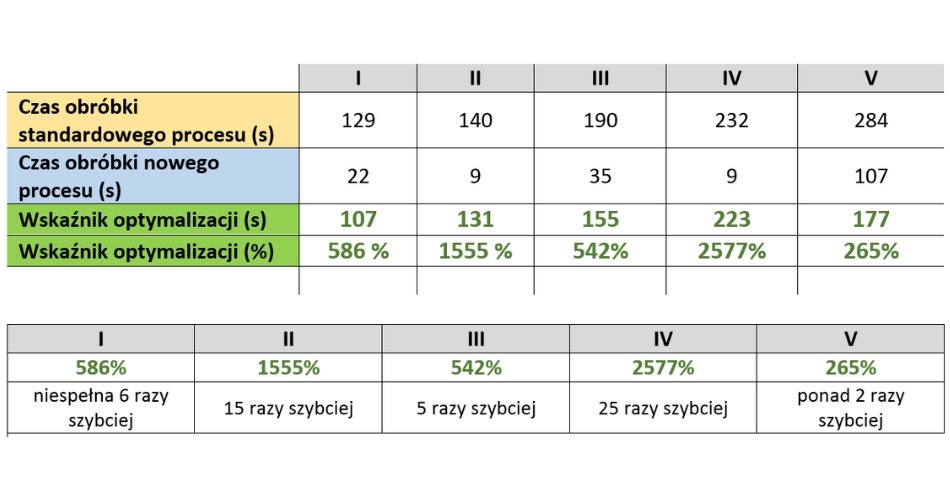
I jeszcze jedno, najważniejsze. Nie powiedzieliśmy sobie czegoś w stylu: „Dobra zrobione, działa i jest OK. Wystarczy”. Rozpoczęliśmy i obecnie koordynujemy współpracę ze światowym liderem branży. Czekamy z mocno zaciśniętymi kciukami na rezultaty dalszych testów.
Podziękowania dla wszystkich, którzy uczestniczyli i uczestniczą dalej w zadaniu, a w szczególności dla koleżanek i kolegów z obszaru modelowania i dygestorium.